
LEAN SIGMA
GREEN BELT TRAINING
October
2024
Class starts
January
2025
Class Wraps Up
February
2025
Project Ends
March
2025
Yield Results
This Certification is an investment in your future Leaders. Participants will gain valuable knowledge, experience, and leadership development through the Green Belt Program. They will lead teams through change to successful results and be able to help your organization embed continuous improvement thinking throughout the company over time.
This training program is rigorous and proven to yield. sustainable results. Throughout the training, participants will execute on a constraint or business pain that results in generating significant financial gains for their organization. The class is also complemented with a very effective coaching process, allowing the
Belt in-training to maximize the results and their learning. Successful Green Belt projects will yield a bottom-line gain of $50K to $175K + with good project selection, which Wavez will assist with.
A full-time Green Belt will yield $350K to $700K+ in bottom-line $ annualized in most companies and even more in others.
A part-time Belt can realize savings of between $200K - $400K+ annually.
Equivalent of 8 Classroom days of Training
8-10 One-on-One Personal Coaching Sessions
Two 3-Hour Group Coaching Sessions
One Green Belt Open Book Test
One 2-Hour Project Defense per participant
Successful Execution of 10+ Green Belt Projects saving a minimum of $50K per project
We target to average $100K+ per project with the classes (varies by organization or business)
Lean-Sigma Green Belt Certification/ Certificate
Training Consists of:
Materials, Files & Books Supplied per list below:
Presentation Material (soft copy)
Keller Statistics Textbook (soft copy)
Black Belt Memory Jogger (PDF)
Our Iceberg is Melting (PDF)
Everything I Learned About Lean, I Learned in First Grade (PDF)
Electronic files (Forms)
Lucid Spark Software for Collaboration (Will use Wavez software for Certification project)
Each Participant receives
Laptop for the Belt
Statistical Software (One-time cost of $300US per user)
Items Your Company will need to Supply

TRAINING MODULES

Module 1
Define and measure
Participants will learn in a highly interactive virtual classroom setting that involves presentations, simulations, table exercises, and role- playing/facilitation. This first Module gets the Belts understanding Targeting and Measuring Performance Improvements with Metrics. The tools below also equip them to understand the As-Is State in detail and where all the problems, challenges and opportunities exist down to root cause levels through waste identification. They will learn how to facilitate the team through each of the tools by making use of them in class through exercises. Expectations will also be set for project progress expected by next class days. The Green Belts In-Training will learn: Project Chartering, SIPOC, Cost of Poor Quality, Project Planning, Baseline Performance, Metrics, Basic Statistical Thinking, Value-added/Non-Value-Added/Value Enabling, Measurement System Analysis, Knowledge Tools (Process Flow-charting, Fundamental Waste Analysis, Fishbone Diagram, Failure Modes Effect Analysis), and how to isolate the relevant issues to focus on for improvement.
The second training module is focused on providing the belts with Lean techniques and where and how to leverage them. They are also trained in methods to implement and control them. This allows the belts to implement improvements early in their projects, building momentum for the team and generating early wins. Topics covered include Leading Change, 8 Fundamental Wastes, 5S+1 (Safety), Future State Process Maps, Pull Systems, Kanbans, Material Flow Techniques, Mistake Proofing, Accelerated Improvement Workshops (similar to Kaizen events), Control Techniques, Control Plans, and Daily Management (Visual Workplace, Management by Walking Around, and Effective Team Huddle Meetings).
Lean analysis, Improve, and Control
Module 2
The third training module is focused on the six-sigma analysis tools, which allows the belts to analyze the “Potential X’s” out of the Measure phase of their project. These are the items that the team has identified as potential root causes, but analysis is needed to confirm prior to proceeding in the implementation of improvements to ensure the investment of time and energy is warranted. Statistical software will be used for these two days. Topics covered include Data Collection Plan, Hypothesis Testing, Parametric and Non-Parametric analysis including: T-test, 2-Sample T-test, ANOVA, Correlation, Simple and Multiple Regression, Mann Whitney, Paired T-test, 1 Proportion Test, 2 Proportion Test. This provides the belts with the vast majority of the essential analysis tools to execute on most projects.
Analyze
Module 3
This module is focused on tools used to develop, implement, and control improvements for items identified as Opportunities-for-improvement by the team and “Critical X’s” from the Analyze phase. There is a thorough review of control plan methods and a full summary review of all material covered in the training. The exam for the Green Belts will be held on the morning of the final day of class and will be a two -hour open-book format.
Improve, Control & Exam
Module 4
Wavez Consulting’s Master Black Belt / Black Belt will provide all coaching for the class participants. Each Belt will have one to two 1-hour individual coaching session between each module and individual coaching after the final class. The coaching will take place within two weeks of the latest training session. There will also be two group coaching sessions held during the timeframe of the training sessions. Coaching is done on-site or virtually and follows a coaching protocol that leaves the belt-in-training with documented coaching notes and feedback at the end of each session. The coach is also available for phone calls, emails, etc. to provide additional support as required. The commitment is for the belts in-training to receive a high level of professional coaching to enable success.
Coaching by a Master Black Belt / Black Belt
Each participant will present their project to Wavez Consulting’s Master Black Belt, showcasing the project and the results that have been achieved. Based on the presentation and results, the belts will be Certified Lean-Sigma Green Belts following the Project Defense.
Defences / Certifications

WHITE BELT TRAINING
We traditionally conduct this training company by company, but we will be offering multi-organization training for White Belt in 2025. We typically do this training in-person onsite. It is an outstanding way to get your team excited about making improvements. We also offer a six (6) hour online version of the training. The white belt is one (1) day of training that can be done in-person onsite or virtually. It is planned for eight (8) to 20 participants for in-person training and unlimited for the virtual version.
It is a highly interactive day session of waste identification and learning the core Lean tools and how to leverage them to make improvements in
their own areas of the business. The participants will also gain an understanding of the Point Improvement process for small or medium size project execution and problem solving, the Accelerated Improvement Workshop (AIW) process for larger projects, as well as Daily Management to manage team day-to-day expectations and performance.
Key Takeaways
Participants come out of this very sensitized to the 8 Fundamental Wastes and can more readily recognize them in work processes on the job
Understanding a simple improvement method to solve problems and make improvement
Trained in Lean-Sigma at a high level. Enough to make valuable use of it at work.
Introduced to Lean Techniques that can be applied at work.
How to facilitate and lead in teams
Formal brainstorming processes and which to use depending on the situation
Seeing how making improvement can be a fun engaging team activity
How to make changes stick
Participants are better prepared to participate in any improvement activities within the business as a team member.
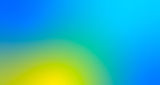
YELLOW BELT TRAINING
We traditionally conduct this training company by company, but we will be offering multi-organization training for Yellow Belt in 2025. If you are interested in having a dedicated session done for Managers, Supervisors and Lead-Hands within your company we can provide this for you at any time. The training is three (3) Days including certification and it can be done in-person onsite or virtually. It is planned for up to 16 participants and the benefits are focused on personal growth, competency plus we target to have each participant save $3K to $5K annualized.
This training includes an interactive two and a half (2 ½) days of training for managers, supervisors, lead-hands. The training is broken down into five (5) two-hour modules The training focuses on equipping the participants with suitable understanding & knowledge of Daily
Management and Lean-Sigma to be able to execute on improvement in their own areas of work using the Define-Measure-Analyze-Improve-Control (DMAIC) process. We provide them with hands-on, in-class experience using the same tools they will use to execute on Just-Do-It’s (JDI’s)
or through participation in medium or larger projects within the company. They will also be given an overview of the Management System, and how the company manages larger and medium sized improvement projects.
As part of this training, each participant will be Yellow Belt certified once they have implemented an improvement in their own area with a write-up of the change, the impact that it will have on the business, and how the gains will be held long term. Wavez will provide the template for the
write-up and there will be a half day for the reviews and certifications.
Benefits
The benefits of this training are, a higher level of improvement activity on a weekly/monthly basis at the department level of your business, led by managers, supervisors and/or lead-hands. This training and certification advance’s the individual problem solving and improvement skill of
those in the training and teaches them best practices in facilitation techniques to properly engage team members in making improvement within their own areas of responsibility. The company benefits by having a more engaged team and improved performance which adds to
the financial performance of the company to generate funds for reinvestment.
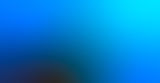
BLACK BELT TRAINING
To date this training and certification has been customized to meet the needs of your organization and assessing this against the current level of competency in Lean-Sigma and Leading Change of the individuals to be trained and certified. A prerequisite to taking Black Belt is being a certified Green Belt, ideally with several projects having been completed to success with good controls in place. In 2025 we will be looking at a small multi-organization training wave, but also welcome the opportunity to upgrade a number of Belts from Green to Black within larger organizations.
Training Days: Eight (8) Days broken down into 16 half-day core modules.
This training can be delivered in person or virtually. There are also 2 days of one-on-one coaching by a Wavez Master Black Belt.
Other Requirements: In addition to the training days, Black Belts must complete a medium to large sized project and hit the targeted improvement level. They must also coach others (Eg. Green Belts) through improvement projects or smaller incremental improvements if there are no others doing projects that could be coached. A significant part of a Black Belt’s role is often coaching others including management on improvement efforts and taking over training such as White Belt Training for their organization, depending on the size and needs of the business.
Body of Knowledge for Assessing Black Belt Development Needs
Enterprise Value Stream Mapping
Strategic Planning
Metrics Development and Management
Lean-Sigma Deployment Management
Building a Library for Process Documentation and Best Practices
Getting to Results Faster through Daily Management and AIW’s
Facilitation Best Practices
Leading Change Best Practices
Coaching (Up and Across and Down within the organization)
Enhanced Daily Management
Refresher on Tools within the DMAIC Methodology
Advanced Statistical tools as required
Control Plan Assessments
Leading a Project to Completion with Results
Learning the Delivery of White Belt and/ or Yellow Belt Training and executing on it
Coaching 2 Improvement Projects / Just-Do-It’s (One of Each) to successful results